Goal and Summary
Orientation of facilities and infrastructure consumes significant time and resources, especially, with power generation plants to ensure office workers as well as plant workers are made familiar with important guidelines which now can be achieved through scanned data that is organized in a manner that can be accessed from various devices securely and navigate with audio / readable instructions in a virtual manner but allow access to limitless number of users to concurrently can eliminate scheduled tours and optimize O&M costs.
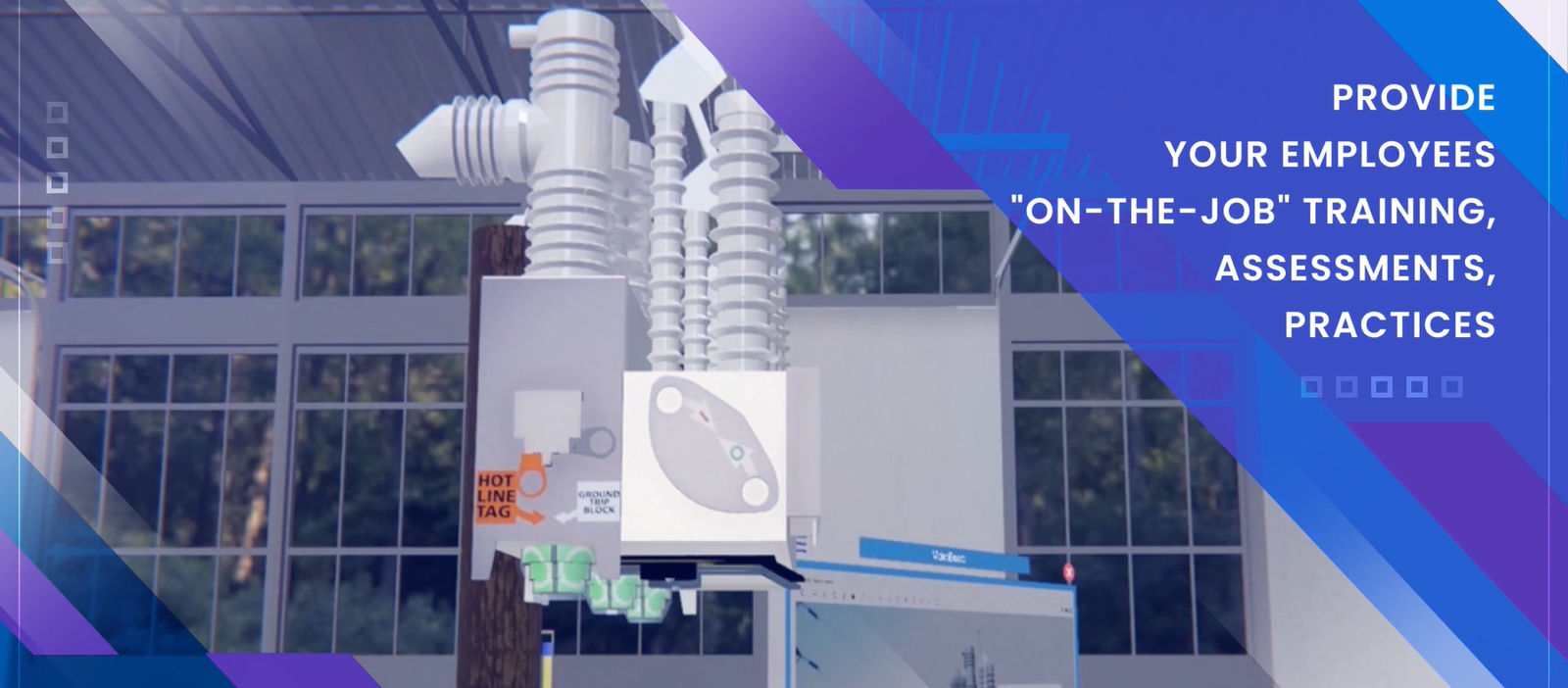
Facility walkthroughs are essential in industries like power generation, where both office and plant workers need to be thoroughly familiarized with the infrastructure, safety protocols, and operational guidelines. However, traditional walkthroughs can be time-consuming and resource-intensive, especially in large or complex facilities. Modern technologies offer innovative solutions to streamline this process, making it more efficient and effective.
Challenges of Traditional Facility Walkthroughs:
Time-Consuming: Conducting physical tours of extensive facilities, especially for large groups, can take a considerable amount of time.
Resource-Intensive: Organizing walkthroughs requires the availability of knowledgeable staff to guide the tours, and it often disrupts normal operations.
Inconsistent Information: Different guides may provide varying levels of detail or focus on different aspects, leading to inconsistent information being shared.
Limited Accessibility: Walkthroughs need to be scheduled, and not everyone may be able to attend, particularly if they are off-site or have conflicting responsibilities.
Safety Risks: In operational environments like power plants, bringing groups through active areas can pose safety risks if not carefully managed.
Modern Approaches to Facility Walkthroughs:
Virtual Walkthroughs and Tours:
- 3D Virtual Tours: Create a 3D digital model of the facility that employees can explore at their own pace. These tours can include interactive elements, such as clickable hotspots that provide detailed information about specific equipment, safety protocols, or operational procedures.
- 360-Degree Video Tours: Record a 360-degree video of the facility, allowing employees to experience a guided tour through their computers or VR headsets. This method provides a realistic sense of the space while eliminating the need for physical presence.
- Digital Orientation Modules: Develop comprehensive digital orientation programs that include virtual tours, diagrams, and instructional videos to familiarize new hires with the facility.
Augmented Reality (AR) Walkthroughs:
- AR Navigation: Use AR apps on mobile devices to guide employees through the facility. The app can overlay digital markers, instructions, and safety information directly onto the real-world view, helping employees navigate complex environments.
- On-Demand Information: Workers can use AR to scan equipment or areas within the facility and receive instant information about safety guidelines, operational procedures, or maintenance schedules.
Interactive Facility Maps:
- Digital Facility Maps: Provide employees with digital maps that are accessible via smartphones or tablets. These maps can include layers of information, such as emergency exits, hazardous areas, and locations of critical infrastructure.
- Self-Guided Tours: Employees can use the interactive map to conduct self-guided tours, accessing relevant information as they move through the facility.
E-Learning Modules for Orientation:
- Safety and Protocol Training: Develop e-learning modules that cover key aspects of the facility’s safety protocols, operational guidelines, and emergency procedures. These can be completed before the physical walkthrough, ensuring employees are already familiar with the basics.
- Quizzes and Assessments: Include quizzes and assessments within the e-learning modules to ensure that employees have understood the critical information.
Remote Assistance and Guidance:
- Real-Time Video Support: For remote workers or those who cannot attend a physical walkthrough, use video conferencing tools to guide them through a virtual or physical walkthrough. Remote experts can provide explanations and answer questions in real time.
- Live Streaming: Stream live walkthroughs for employees who are off-site, allowing them to participate remotely and interact with the guide.
Benefits of Modern Facility Walkthroughs:
- Time and Cost Efficiency: Virtual and digital methods reduce the time and resources needed for orientation, allowing for more frequent and flexible onboarding.
- Consistency and Accuracy: Standardized digital content ensures that all employees receive the same information, reducing the risk of inconsistent messaging.
- Enhanced Safety: Reducing the need for physical presence in operational areas minimizes safety risks during the orientation process.
- Accessibility and Convenience: Employees can access orientation materials at their own convenience, from any location, ensuring that all workers, including remote employees, are familiarized with the facility.
- Scalability: Digital walkthroughs can easily be scaled to accommodate larger groups or multiple locations, making them ideal for large organizations with extensive facilities.
Application in Power Generation Plants:
In power generation plants, these modern approaches can be particularly beneficial due to the complexity and potential hazards present in such environments. For example:
- AR-enabled safety walkthroughs can guide plant workers through critical areas, ensuring they understand the specific hazards and safety procedures associated with each zone.
- Virtual tours can help office workers understand the operational side of the plant without needing to physically enter high-risk areas.
- E-learning modules focused on plant-specific safety protocols can ensure that all employees, including temporary workers, are fully briefed on emergency procedures before they ever set foot in the plant.